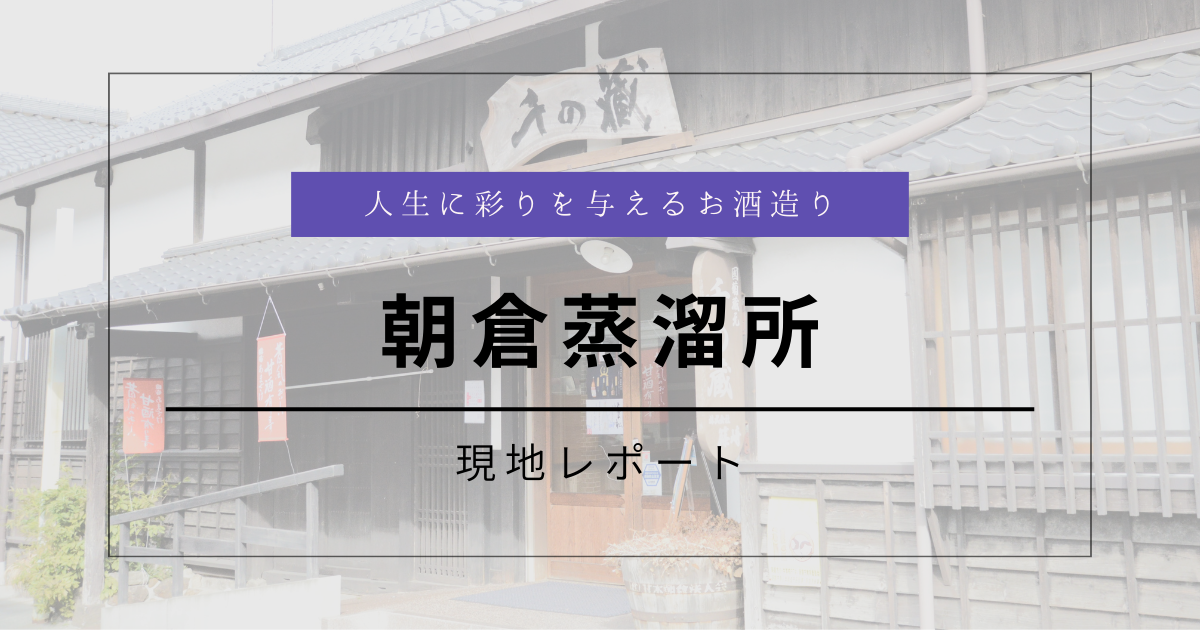
【現地レポート】江戸から続く伝統を礎に、自由な発想をもとに挑戦を続ける朝倉蒸溜所
- 造り手
- 蒸溜所(日本)
2024.10.18
ウイスキー好き必見の コンテンツが盛りだくさん! | 未加入 | Dear WHISKY 無料会員 | ||
---|---|---|---|---|
ウイスキー 知識情報 | 最新ウイスキー情報を最速でお届け!世の中にはない会員限定情報も?! | ✔ | ✔ | |
蒸溜所情報 | 新興蒸溜所から馴染みの蒸溜所まで、余すことなくお届け! | ✔ | ✔ | |
ボトル情報 | 数多とあるウイスキーの情報を徹底リサーチ!あなたにおすすめのウイスキーが見つかるかも?! | ✔ | ✔ | |
Bar情報 | 旅行先で、ふとBarに行きたい時、穴場から王道までご紹介! | ✔ | ✔ | |
会員限定記事 | 「DWの会員の方なら」と関係者から聞くことができた、ほかでは決して手に入らない情報をお届け! | ✔ | ||
Bar特典 | 世界各国のbarで使える会員限定特典が盛りだくさん! | ✔ | ||
オーナーズカスク 割引特典 | 「自分だけのウイスキーが欲しい…」ウイスキー愛飲家の願いを叶えます!会員限定特別価格でご提供! | ✔ | ||
造り手交流会や イベント案内 | 造り手同士でも、造り手から飲み手でも、会員の皆様へ特別イベントをご招待! | ✔ |
下記からログインを行うか、新規会員登録をお願いいたします。
ウイスキー知識を発信し続けて約2年が経過した Dear WHISKY は、
2024年夏に更なる進化を遂げここでしか得られない情報を惜しみなく発信します!
詳しくはこちらから!