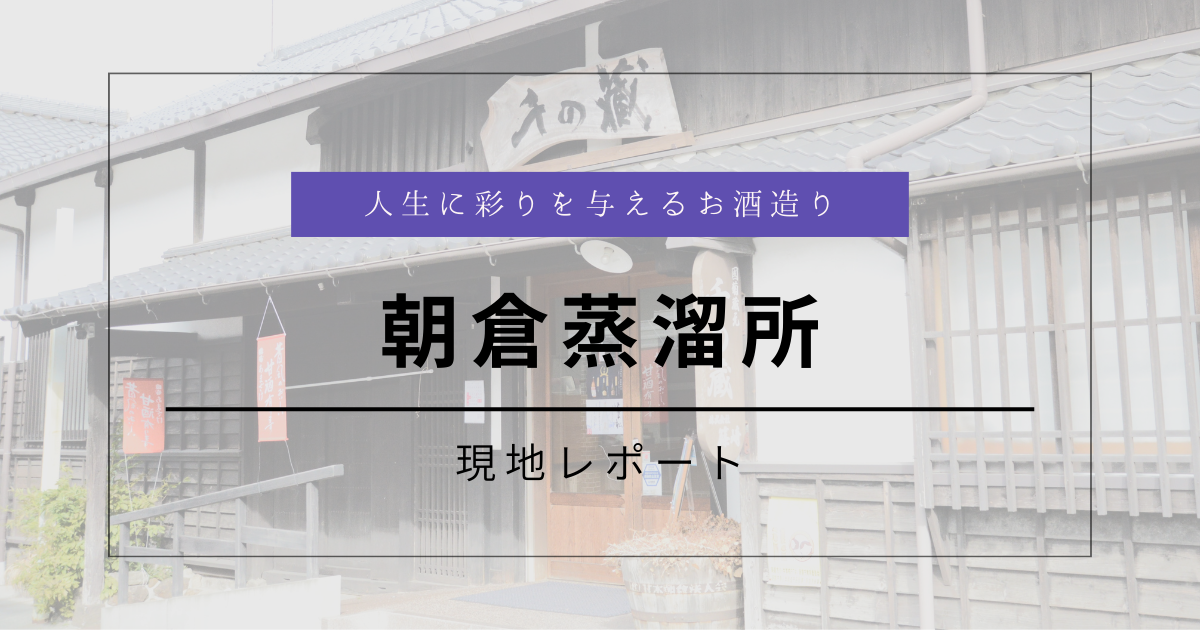
【現地レポート】江戸から続く伝統を礎に、自由な発想をもとに挑戦を続ける朝倉蒸溜所
- 造り手
- 蒸溜所(日本)
スコッチウイスキー文化の中心地であるスペイサイドに位置するForsyths社(フォーサイス社)は、蒸留機器メーカーとして1世紀以上にわたりウイスキー業界の柱となってきました。
卓越したポットスチルの製造技術と顧客中心のアプローチで世界的に知られ、4世代にわたる家族経営の中で、世界中のウイスキー業界に独自のマーケットを切り開いています。
今回Dear WHISKYは、リチャード・フォーサイス会長直々に、Forsyths社の工場を案内していただきました!
Forsyths社の工場が一般公開されるのは、スピリット・オブ・スペイサイド・ウイスキー・フェスティバル期間中の数日間だけで、Forsyths社の工場の様子は中々見ることができません。今回の記事は、世界最高のポットスチルメーカーの製造工程について解説した貴重な記事となっていますので、せひ最後までご覧ください!
【独占インタビュー】第1弾: 創業130年の老舗蒸留機器メーカー、Forsyths社の現会長リチャード・フォーサイスさんにインタビュー!
【独占インタビュー】第2弾: 創業130年の老舗蒸留機器メーカー、Forsyths社の現会長リチャード・フォーサイスさんにインタビュー!
会社名 | Forsyths社 |
創設者 | アレクサンダー・フォーサイス |
住所 |
Forsyths, Rothes, Moray, Scotland, AB38 7AD
|
創設年 | 1890年 |
公式HP | 公式HPはこちらから! |
1890年にアレクサンダー・フォーサイスさんによって設立されて以来、Forsyths社は世界有数の蒸留機器メーカーとして成長してきました。
Forsyths社が愛される大きな理由の一つは、献身性と信頼性の証でもある、4世代にわたる家族経営です。
ターンキーサービス(※)を筆頭とする、同社の幅広いサービスと製品は、単なる設備の製造に留まらず、設計から建設まで蒸溜所開設の全てを網羅しています。
ターンキー(鍵を回す)するだけで、すぐに使用できる状態で設備を納品することを指す。
今回、Dear WHISKYは光栄にもForsyths社の会長であるリチャード・フォーサイスさんに工場内を案内していただきました。リチャードさんは12歳から父親の工場を手伝い始め、16歳で学校を卒業した後に正式にForsythsへと入社しました。
リチャードさんはもう60年近くForsyths社で働いています。
リチャード・フォーサイスさん
リチャードさん:
Forsyths社は1972年、ロセスの中心に位置する、閉鎖された駅構内を利用して建てられました。
創業当時は小さな工場にすぎませんでしたが、今では付近にあったキャパドニック蒸溜所を買収し、取り壊して工場を拡張するほどにまで成長しました。
キャパドニック蒸溜所の倉庫は今でも残っており、約14,000樽を貯蔵することができます。
リチャードさん:
ここは、あらゆる機器の図面を作成するためのオフィスです。 流れとしてはまず最初にクライアントと会い、サイズと形状について話し合い、必要な銅の量を割り出すための図面を作成します。
現在、私たちは主に5,000Lのポットスチル (4人掛かり、8週間で組み立てる) から、最大50,000Lのポットスチル (12人掛かり、20週間で組み立てる) まで製造しています。
リチャードさんとその後ろにあるオフィスビル
リチャードさん:
やはり銅の柔軟性のためでしょう。
柔らかいため、丸めたり、切ったり、形を整えたりするのが熟練した職人の手にかかれば比較的容易です。
スコットランドの禁酒時代でも、小型のポットスチルをつくるにはよく銅が使用されていて、それが今でも伝統となって大切にされているのです。
職人の手にかかれば、銅を手打ちすることも可能です
リチャードさん:
何度もステンレス製のポットスチルを試すうちに人々は、銅が蒸留工程に不可欠な要素であることに気づきました。ステンレスのポットスチルではまともな蒸留酒を製造することができず、硫黄臭を除去するという銅固有の能力が浮き彫りになりました。
これらの臭いは高品質のウイスキーには望ましくないとされ、銅はウイスキー製造に欠かせないものとなりました。
ポットスチルのほとんどの部品が銅でできています
リチャードさん:
我々は100トン単位で銅を仕入れており、その大部分はドイツの銅工場から来ています。これらは、用途に応じて3ミリから10ミリまで、さまざまな厚さのシートになっています。ポットスチルは主に7つの部品で構成されており、製造には7枚のプレートが必要です。当社が使用する銅はすべて純度99.9%の銅であるため、ポットスチルとして使用された後、ほとんどがリサイクルされています。
銅は光沢があり、きれいにカットされた状態で届きます
リチャードさん:
銅板とオフィスでデザインされた図面をあわせ、この装置で50,000psiの高圧ウォータージェットを使用し切断します。この装置は、厚さ6ミリまでのプレートであれば完璧に切り出すことができます。余った部分の銅は工場に戻され、リサイクルされます。
図面に合わせてプレートをきれいに無駄なく切断します
リチャードさん:
大きな部品を丸めて円錐形に形成し、溶接してその部位の簡単なシルエットを形作ります。
カットした銅を奥のローラーを使って丁寧に丸めます
リチャードさん:
昔はハンマーを使いすべて手作業で行われていましたが、今では大型のハンマリング用の機械が導入されています。
工程はほぼ同じです。基本的にブラックスミス(鍛冶屋)のように、金床を内側に置き、外側からハンマーで叩きます。我々の場合は、ブラックスミスではなくコッパースミス(銅を加工する職人、銅細工師)ですね。
大きなものは二人がかりで丁寧に叩いていきます
リチャードさん:
銅は柔らかい金属のため、焼きなましするとしっかりその状態が維持されます。これは実用的ではあるものの、耐久性に欠けたものが出来上がってしまいます。
したがって、仕上げを行う他に、再度強化するためにもハンマーで叩いているのです。
ピットホール(下の穴の部分)はスペイサイド地方、最大のポットスチルでも入るように設計されています
リチャードさん:
機械はあるものの、ハンマーで叩く作業の多くは依然として手作業で行われています。
ここでは、ポットスチル周りのカーブなどを木型を使いつつ測りながら、手で形を打っている様子が見られます。
手作業で正確にハンマーで叩き、木製の型で曲線の角度を測定
リチャードさん:
ご覧のとおり、大きな部品はここで組み立てられて溶接されます。溶接の後、中には、溶接した後にもう一度ハンマーで叩く部品もあります。すでに美しい形が見受けられますね。
部品は組み立てられる前にそれぞれ、全く違ったプロセスを経ます
リチャードさん:
ここでは、今でもさまざまな種類や大きさのポットスチルを見ることができます。
ここにあるのはすべて出荷を待っている新品のポットスチルです。
表面の変色はターニシングと呼ばれるもので、出荷前に希硫酸で洗浄します。これは酸化によって引き起こされるため、洗浄後に特殊な薬剤を使用し、酸化を防ぎ本来の色を維持します。
横向きに置かれたポットスチルなど、Forsythsの工場でないと見る機会がないでしょう
リチャードさん:
ポットスチルの摩耗速度は、各部品ごとに異なります。たとえば、ウォッシュスチルの場合ヘッド、ネック、コンデンサーの部分が最初に摩耗しますが、スピリットスチルの場合だとバルジが最初に摩耗します。これは、初留の際に造られるローワインに固体が含まれているため、非常に揮発性が高く、銅に多くの負担がかかるためです。
部品は別々に作成され、組み立てられるのを待っています
リチャードさん:
したがって、Forsythsのメンテナンスプログラムの一環として、我々は毎年すべての顧客を訪問し、ポットスチルの厚さをテストします。
昔は超音波検査器がなかったため、父はポットスチルをハンマーで叩いて検査していました。
目安としては、元の厚さの半分になったら、交換を検討する必要があります。
リチャードさんがポットスチルを叩く方法を教えてくださっている様子。奥には伝統的な木製ウォッシュバックがあります
リチャードさん:
このセクションではステンレス製のウォッシュバックを製造しています。現在、ステンレス製のウォッシュバックが非常に人気ですが、Forsythsでは木製のウォッシュバックも製造しています。
ウォッシュバックやマッシュタンのさまざまな部品を別々に作成し、この自動溶接機を使って溶接します。
製品をターンテーブル上に置き、ゆっくり回転させながら垂直方向と円周方向に溶接します。
ステンレス製ウォッシュバックを自動溶接機で組み立てている様子
リチャードさん:
ここでは蒸溜所内の細かな同線に使用される、さまざまなパイプ類も製造されています。信じられないかもしれませんが、蒸溜所設立の大部分がこのステンレスパイプの配管作業になります。
Forsyths社は、最小のパイプに至るまで、蒸溜所内のあらゆるものを製造しています
さらにリチャードさんは、Forsyths社が所有するステーションホテルにも私たちを招待してくださいました!
ホテルはウイスキーをテーマにデザインされており、各部屋には蒸溜所の名前が付けられています。内部のあらゆる細かな装飾にも銅が使用されていて、どことなくポットスチルを思わせます。
ウイスキーキャビネットにリメイクされたスピリットセーフ
ホテル内にあるバー「スピリットセーフ」には、世界中から集めた500種類以上のウイスキーとジンが揃っています。メニューには、多くの閉鎖蒸溜所を含むとても希少なウイスキーが揃っています。
バーカウンターの下にあるエンブレムは、半径80キロ以内にある60の蒸溜所のポットスチルを表しています。
蒸留プロセスの技術進化と近代化が進む中、Forsyths社のポットスチル製造方法は造り手の伝統と効率的な機械化が組み合わされています。
世界一の生産能力と事業規模にもかかわらず、Forsyths製の蒸留機器のほとんどは、あらゆるプロセスを通じて多くの職人によって手作業で造り上げられています。
工場内を見学すると、極小のパイプから巨大なポットスチルまで、文字通り蒸溜所に必要なものすべてを目にすることができました。このような幅広いサービスを提供するようになった経緯を、インタビュー記事にてリチャードさんからご説明いただきました。ぜひ併せてお読みください!